
About Pyrosin
About Pyrosin
Pyrosin is heat resistant paint which is able to prevent corrosion of metal surface by creating heat resistant paint film mainly on surface of steel materials. Pyrosin has been used in various fields such as Engineering plants, Chemical companies, Automotive sectors, Home appliances, etc, for more than 75 years since putting on market. We are proud of Pyrosin`s highest quality and reliance in the paint industry by obtaining a good reputation among its users in the world.
The General Feature of Pyrosin
- 01.Pyrosin has great heat resistance.
- 02.Pyrosin has good adhesion strength and keeps paint film in a good condition for a long time.
- 03.Pyrosin has great weather-proof and anti-ultraviolet radiation and any chalking would not happen in most of time.
- 04.Pyrosin has great heat resistance.
- 05.Pyrosin has great anti-corrosion performance, especially LL type Pyrosin withstand for long period exposure, is suitable for new plant and export plant.
- 06.Pyrosin has good coating properties.
The Line up of Pyrosin
- 1. General Heat Resistance
- This paint is used or the general plant of which machinery is installed n outside or inside of the building under usual circumstance and continuously operates. It can be used under some acid and alkaline circumstance.
- 2. Thermal Shock Resistance
- This paint is designed to endure thermal shock and can withstand under big temperature change during operation and frequent stoppage of machine happens.
- 3. Heat Resistance & Chemical Resistance
- This paint is designed to have chemical resistant performance in addition to heat resistance and can protect the painted steel from corrosion due to acid and or alkaline gas in high temperature.
- 4. Heat Resistance, Waterproof & Chemical Resistance
- The paint is designed to have heat resistant, water proof and chemical resistant performances and can significantly improve its anti-corrosion performance under existence of condensed water and vapor.
- 5.Boil Water Resistance
- The paint is applicable to inside of hot water and steam tank used for boiled water also can protect the iron surface from very sever conditions of high temperature / high humidity and acid circumstance.
The Type of Pyrosin
- ○ For motor vehicle (CX type) Mufflers for motorcycles and automobiles, Exhaust pipe, Brake disk.
- ○ For stove(SX Type) Stove, Fan heater louver, outside of combustion cylinder
- ○ For kitchenware(KX type) Hot plate, rice cooker, Table stove, frying pan, oven, ironware(mold)
- ○ For gas fitting Gas table, Burner cap, Gridiron, Tripod, Fish roaster, and so on.
- Expected durable years: less than 3 years.For plant
- Expected durable years: less than 5 years.For plant
- Expected durable years: less than 7 years.For plant
- Rapid heating specificationFor plant
- Chemical resistance specificationFor plant
- Boiling water resistanceFor plant

Usage example of Pyrosin(Blacked out white background indicates inside.)
Usage example of Pyrosin at an incineration facility
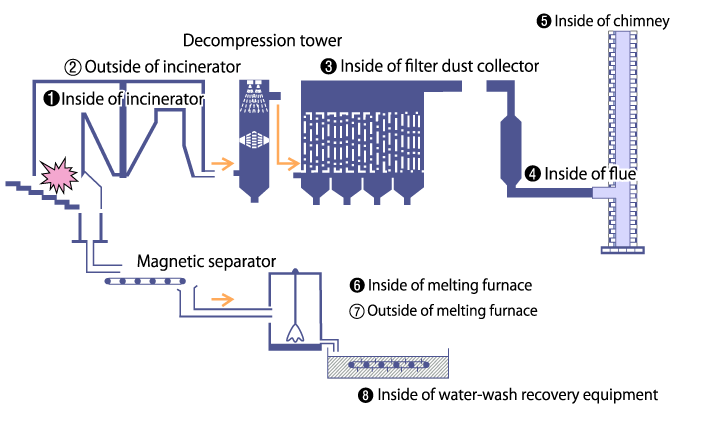
Usage example in incineration system
- ❶Inside of incinerator: Stack ACT#250A with hardener
- ②Outside of incinerator: Undercoat XZ-180-3 Last coat B#900 Silver
- ❸Inside of filter dust collector: Stack ACT#250A with hardener
- ❹Inside of flue: Stack ACT#250A with hardener
- ❺Inside of chimney: Stack ACT#250A with hardener
- ❻Inside of melting furnace: Stack ACT#250A with hardener
- ⑦Outside of melting furnace: Undercoat XZ-180-3 Last coat B#900 Silver
- ❽Inside of water-wash recovery equipment: Inner 7(3-5 liquid type)
Usage example of "Pyrosin" at power facilities (oil, gas)
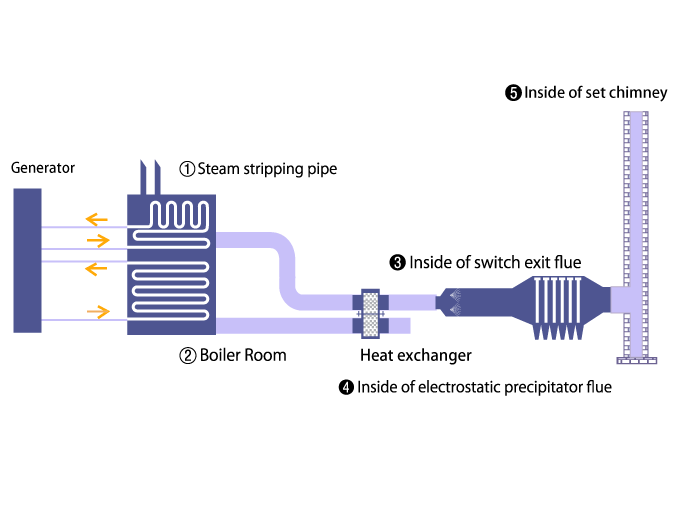
Usage example at power facilities
- ①Steam stripping pipe: Last coat B#l000-22 with silver hardener
- ②Boiler Room: Undercoat XZ-180-3 or XZ-180-7 Last coat B#900 Silver or B#850 Silver
- ❸Inside of switch exit flue: ACT#250A with hardener
- ❹Inside of electrostatic precipitator flue: ACT#250A with hardener
- ❺Inside of set chimney:StackACT#250Awith hardener
Usage example of "Pyrosin" at steel production facilities
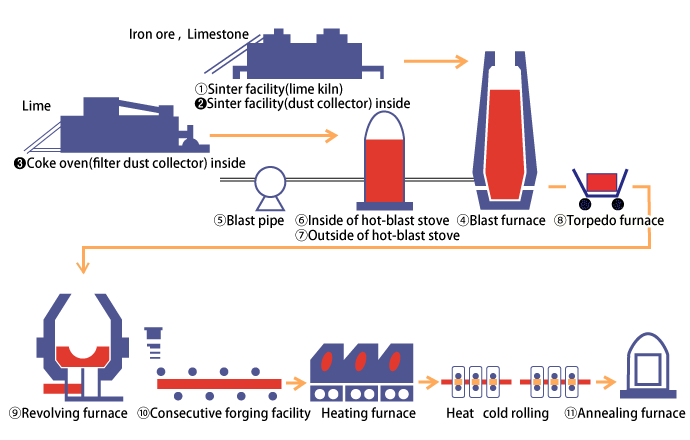
Usage example in steel production facilities
- ①Sinter facility (lime kiln): Undercoat XZ-180-4
Last coat B#1000-22 with silver hardener - ❷Sinter facility (dust collector) inside: Stack ACT#250A with hardener
- ❸Coke oven (filter dust collector) inside: Stack ACT#250A with hardener
- ④Blast furnace: Undercoat XZ-180-4 Last coat B#1000-22 with silver hardener
- ⑤Blast pipe: Undercoat XZ-180-4 Last coat B#1000-22 with silver hardener
- ❻Inside of hot-blast stove: Stack ACT#250A with hardener
- ⑦Outside of hot-blast stove: Undercoat XZ-180-3 Last coat B#900 silver
- ⑧Torpedo Car: Undercoat XZ-180-4 Last coat B#1000-22 with silver hardener
- ⑨Revolving furnace: Undercoat XZ-180-4 Last coat B#1000-22 with silver hardener
- ➉Consecutive forging facility: Inner 7 (3-5 Liquid type)
- ⑪Annealing furnace: Undercoat XZ-180-3 or B#500 Primer Last Coat B#900 Silver or B#500 silver
Application of Pyrosin
Application 01
Coating Environment
Please do not apply under the following conditions as they may effect badly to the drying/forming of the coating film.
- ①When rain or snow is expected.
- ②When the temperature is lower than 5℃ or within 3℃ of dew point. (When condensation occurs)
- ③When the relative humidity is over 85%.
- ④On a windy day.
Materials
The materials have heat resistance, and the heat resistant paint demonstrates its heat resistance and rust-prevention power in this range of temperature.
- ●Common steel plate / to approximately 600℃
- ●Stainless steel / to approximately 650℃
- ●Electro galvanized zinc plated steel / to approximately 280℃
- ●Aluminized sheet / to approximately 480℃
Surface preparation
Since heat resistant paint tolerates expansion and contraction caused by thermal strain, the quality of surface preparation largely affects the coating performance. *Please conduct adequate surface preparation according to each specification.
Coating
Because heat resistant paint uses heavy pigment, it may be settled in the can, so please use after string it with a hand mixer and confirming there are no sediments in the bottom. Stir it each time when subdividing to hanging buckets.For multi-liquid mixing type, compound and stir upon consideration of mixture ratio, working life, and amount.
Coating method
Brush application, airless spray, and air spray are popular and recommended methods for heat resistant paint. Features for each method is as follows. *The coating could foam when using a roller brush, so be sure to use a non-foaming roller.
Application 02
Film thickness
Please apply the coating according to the standard film thickness set for each coating. Please note that the film thickness shown is not the minimum film thickness.
- [In the case of thin film]
- There are risks of poor appearance and lowering in rust prevention power.
- [In the case of thick film]
- There is a risk of lowering in heat resistance.
Coating interval
Please keep the coating interval when recoating. When the coating interval is long (medium exposure, long exposure types), remove extraneous matter (salt, oil, etc.) with a power tool or a rag.
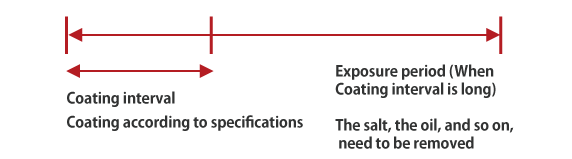
Drying / Baking
Please arrange a curing period of more than 3 days for cold setting coating.The temperature and time for baking indicates the temperature and time of the coated matter.
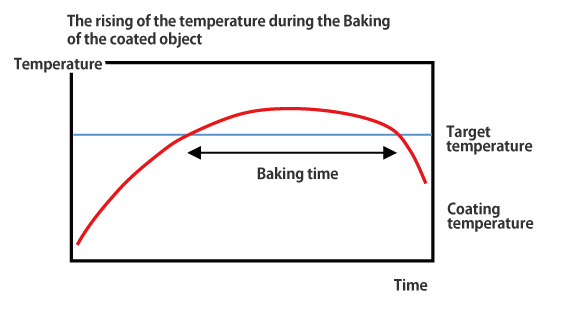
- [Heating initial]
- Since when the Heat-resistant paint is initially heated, Blistering may occur due to the residual solvent during the coating film and the reaction gas when the coating film is cured; the initial heating should be kept to 200℃ / h or less as much as possible.